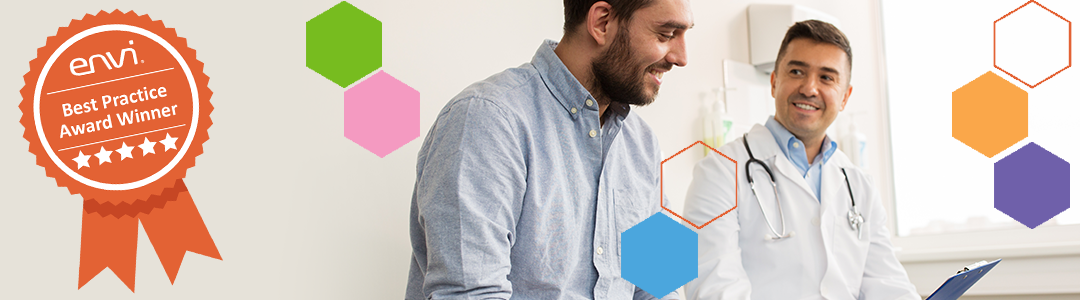
One Medical is the largest independent primary care practice in America, with 72 offices in 9 major areas across the country. One Medical uses technology as a key strategy in advancing business, from seamlessly connecting patients with providers, to streamlining and supporting the infrastructure of the entire enterprise.
Faced with rapid expansion, the supply chain team set about consolidating separate systems and processes, streamlining manual AP processes to digital, and increasing accuracy and automation throughout the enterprise.
THE ONE MEDICAL STORY
Enterprise-wide Standardization Needed
As One Medical experienced rapid growth, the need to streamline and consolidate separate supply chain systems and processes to a single platform became clear. “As we grew, we faced multiple systems in different locations with products and vendors that weren’t standardized,” said Laura Arthur, National Supply Chain Manager, One Medical. “We needed to increase automation in our internal systems and processes. Our AP processes were all paper; invoices were manually scanned, hand coded and then submitted for approval. We needed to streamline all in-office processes for our field teams and allow everything to move more quickly, with greater accuracy.”
Supply Chain Levers to Improve Enterprise Processes
Understanding that supply chain was a strategic lever to achieving overall goals, Arthur and team set about identifying an inventory management and procurement system that could scale, ultimately selecting Envi. “We looked at all internal procedures and used the Envi implementation as time to review and improve existing processes.”
The team built a two-pronged approach around inventory management. Now, supply chain is supported by a central team maintaining core systems, processes, and item master, with local team members managing local ordering and restocking. “This takes the administrative burden off of our clinicians by ensuring our clinical teams always have what they need for patient care,“ said Arthur.
“For consistency and quality, we maintain an item master in Envi used by all locations, containing pre-vetted suppliers and preferred products. We use punch out for one-offs and special circumstances. Patient safety is supported as locations use pre-approved supplies, and we benefit from cost savings using the same vendor partners across the country.”
Envi allows the One Medical team to standardize processes and improve compliance. “We train our team members continuously and are vigilant about continuous improvement.
We strive to ensure our teams know exactly what to do, why and how to do it, and how their role supports patient care. At the end of the day, our goal is to offer acceptable, affordable care to everyone, and each of our employees helps serve this goal.”
Envi Drives Best Practices
As One Medical completed their national roll-out of Envi, Arthur added advice from her experience with the Envi solution and new supply chain processes. “Invest early in
the quiet background foundation of systems and support, so clinical teams can focus on exceptional patient care. We take administrative work off the clinician’s plate by having a local team member in every office fully trained on Envi, to manage inventory and stock the office. With less burden, clinicians focus on engaging, meaningful interactions with patients.”
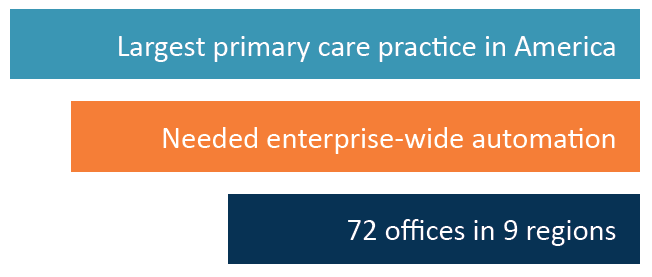
The supply chain team has identified and measured benefits in a number of areas. “We’ve seen benefits throughout this process, for example, we’ve reduced the amount of onhand stock and increased product turnover, helping reduce product expiration rates,” said Arthur. “Our offices have seen up to 10% reductions in on-hand supply costs and improved cash on hand through lower inventory. We’re streamlining and standardizing the number of products in each office, saving time for our local teams, and using our space better. With the data we now have available, we’re making better financial and purchasing decisions. Finally, we’re seeing labor savings throughout and especially in AP, by reducing manual activities.”
“Ultimately, Envi gives our team peace of mind as we know our locations have what they need, where they need it, when they need it and that we’re making the best purchasing decisions possible so that we can deliver on our mission of delivering the highest quality affordable care for all.”
Best Practice Award Highlights
- Leverage Envi reporting tools to track PO history and
compliance, support physical counts - Align supply chain and finance
- Automate AP workflows, eliminating manual, paper-
based processes - Reduce clinician’s time spent on supply management
- Perform continuous internal training focusing on process and technology
- Create scalable, standardized new office launch process
The supply chain team at One Medical notes the significant process improvements made using Envi across the enterprise. Arthur concluded, “Envi helps us incorporate more Lean methodologies, for example, we’ve begun implementing Kanban two bin systems in several areas and plan to roll that out across the country. We’ve had a lot of success using the Envi AP module and reporting capabilities. The support we’ve received from the Envi team throughout the entire process has absolutely helped us achieve best practice level processes.”