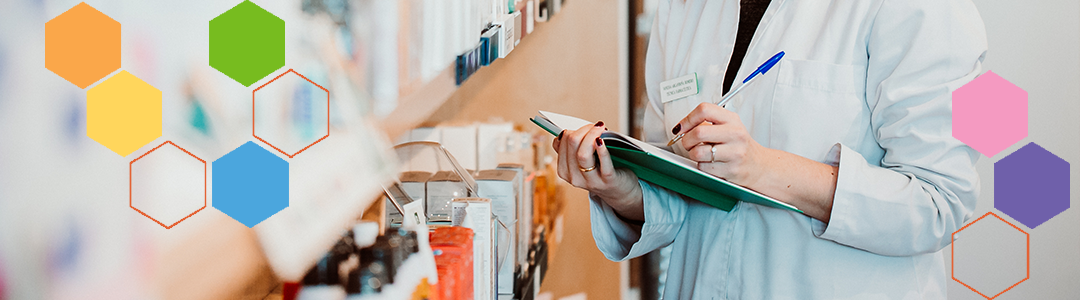
As a distinctively designed ambulatory center, Mercy River Hills Surgery Center is equipped with high-definition, digital arthroscopic equipment to perform over 4,000 orthopedic procedures and pain management treatments each year. Mercy River Hills is jointly owned by Iowa Ortho and Mercy Hospital and has the Joint Commission on the Accreditation of Healthcare Organizations Gold Seal of Approval.
With their implementation of Envi, Mercy River Hills Surgery Center was able to improve, not just automate, their supply chain processes. A cross-functional team identified ways to reduce burdensome manual tasks, simultaneously streamlining them and creating greater visibility.
THE MERCY RIVER STORY
Manual Tasks Meant More Work
Mercy River Hills Surgery Center experienced supply chain challenges that came from using paper-based processes, which in turn increased manpower requirements. Working with handwritten purchase orders (POs), the team lacked a system to capture what was being ordered or received. “There was a huge amount of paper shuffling, as we would manually match paper invoices to POs and packing slips or receipts,” said Bridget Weaver, MHA, Director of Surgery at Mercy River Hills Surgery Center. “Manual processes mean more chance for human error, and I often felt concerned we weren’t accurately reflecting our inventory. In addition, these processes meant we couldn’t be confident in the prices we were being charged, or the prices that were in our system. With prices changing frequently, it was a huge undertaking to update all our pricing manually, so we limited to doing it once or twice a year.”
A cross-functional team of decision-makers worked together to identify a solution. “We knew we needed a system that could eliminate old manual processes and we found Envi,” said Weaver. “As soon as we made the decision, the Envi team helped get our conversion underway. They were instrumental in helping us – they had everything mapped out and ready to go. Our implementation manager did everything from getting our data uploaded to helping set up our inventory areas more efficiently.”
The organization set goals to improve, not just automate, processes. “We wanted not only to replace burdensome manual processes, and but we also wanted to streamline and create more visibility,” said Weaver. “Specifically, we wanted to increase accuracy around our inventory, so we could manage items better and ultimately ensure we were paying correct prices. Additionally, we made it a priority to be able to do case costing for surgical cases.”
Replacing Manual Tasks with Automated Processes
During their implementation process, Mercy River Hills converted from their previous item master to Envi’s item master capabilities. Weaver noted, “We manage everything
more easily in Envi. When we issue a purchase order, it comes back with a confirmation on the price, or an alert if the price doesn’t match. We can identify pricing issues at the time of PO confirmation or when we receive the invoice, and Envi asks if I want to update price in my item master. We update prices throughout the year, which is very helpful with the constant changes in items and prices.”
The surgery center now manages perpetual inventory. “We do an annual physical count, with quarterly spot check counts to verify totals,” said Weaver. “We receive in incoming
supplies and deplete items as we use them, making our ongoing inventory counts much more accurate. We’re improving our communication around usage and consumption
and reflecting depletion of inventory. Our inventory coordinator uses the Envi mobile app to make inventory management and replenishment easier.”
Envi Drives Best Practices
Mercy River Hills Surgery Center has achieved significant results with Envi. “We’ve reduced the time needed to manage purchasing and inventory processes, and increased
price transparency and accuracy. We created a more accurate inventory system, with more accurate reporting of inventory dollars, our financial reporting is far more accurate.
We use Envi to create an end of month accrual log– I can extract a report from Envi and submit to finance without having to do a separate excel file.”
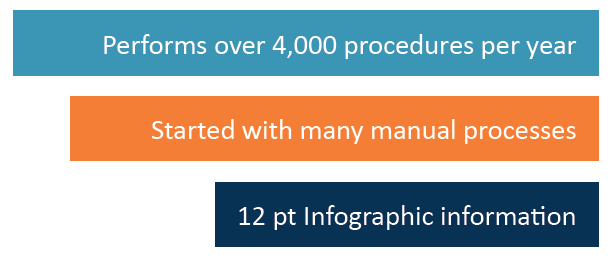
Today, the organization recognizes benefits from improving the receipt of incoming products. “Everything has to be received to pay an invoice,” said Weaver. “Previously, we didn’t have good tracking of backorders or items not yet received. You could get an invoice for a product you hadn’t received and there was a chance the invoice could get paid. It was labor intensive to verify receipt of items – that’s all greatly improved with Envi.”
“In addition to improving the way we handle receiving and inventory, we’ve also improved processes around purchasing approvals. Previously, I manually approved paper POs, but now, we manage approvals through Envi. We’ve reduced time and one-offs.”
Best Practice Award Highlights
- Implement perpetual inventory management with spot
checks and annual physical count - Initiate processes to improve price accuracy
- Ensure accurate contract pricing and alignment
- Perform case costing for specific cases
- Enable automatic invoice matching for accurate payment processes
- Leverage usage reports help with trending, planning
and forecasting - Improve invoice approval process automation
- Advance inventory management processes, improving
item receipt and depleting items as consumed
The Mercy River Hills cross functional team is still working on additional improvements. Weaver noted they will expand their use of Envi’s reporting features and advance their efforts around physician and case costing, helping provide greater financial information for planning and success.