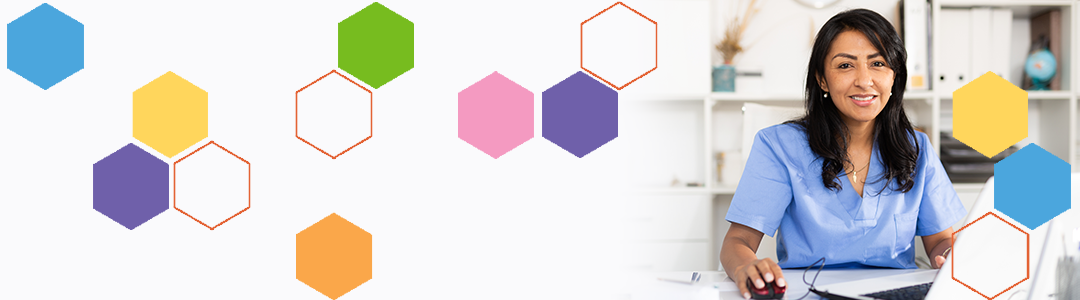
Using a warehouse or central supply area for inventory and fulfillment? A smart step is to implement requisitioning software to drive automation and accuracy for your clinical staff and other end users. You’ll see immediate benefits, like improving inventory levels, eliminating error-prone paper processes, increasing on-contract purchasing, and gaining visibility to supply use by department. And did we mention it will save staff time on every order?
If you’re already using Envi, the Requisitioning module makes it fast and easy to get started. Here are a few steps to help get you started:
1. Decide how you’ll distinguish requisitioning requirements from ordering requirements. In many organizations, requisitions are used to support the needs of supply chain’s internal customers – clinicians and end users, the team members who request products and supplies for patient care in their clinical areas.
Meanwhile, ordering is often limited to authorized Supply Chain/Materials team members, and involves ordering supplies directly from vendors. For many organizations, ordering processes include sourcing, negotiations on price and terms, contract management, quantities and consumption, inventory management, packaging and delivery requirements, and shipping terms.
2. If you’re using Envi, the Requisitioning module will support your central supply requirements and streamline ordering, while also making it easy for clinicians to start using reqs for replenishment. Back in the warehouse, central supply staff members can easily fulfill reqs using their smart device, instead of managing paperwork and having to hunt for missing information.
3. Ready to start? Create department-specific requisition templates for each area. If you’re using Envi, it’s easy to make sure your formulary is up-to-date with on-contract items.
By creating department- or location-specific templates, clinicians and other end users can simply fill in an electronic requisition for the products they most frequently purchase, directly from your approved formulary. You’ll see system-wide cost reductions, plus increase your visibility to consumption.
4. Now you’re ready to set up your electronic approval processes, along with approval process for non-contract items, so non-stock requests can be identified and managed. Even though requisitions for products and supplies are built on your formulary and easily approved, it’s best practice to use approval workflow for tracking.
5. Take a physical inventory in your central supply area for a solid baseline. From here, you’ll be able to track demand for the supplies your team needs while improving tracking, so you’ll see what each department actually requests and consumes.
By managing inventory levels in central supply, you’ll build consumption data over time. This will help manage inventory levels based on annual consumption data. You’ll see annualized trends including seasonality, which will help reduce overstocking and waste of expired products.
Requisitioning helps align processes between central supply / warehouse areas with clinicians and other end users across the organization. This helps improve overall supply chain management processes, reduce overstocked inventory and associated costs, improve budget planning and forecasting, reduce staff time and increase on-contract purchasing. With requisitioning processes running, Envi reporting tools will capture charges for each department, so you can track by facility, department or service line. Better visibility means you can compare department expense to budget and improve forecasting based on more accurate data.